Rapid Warehouse and Industrial Floor Repair Services
Beton911 quickly fixes your concrete floors
Repaired floors can be open to foot traffic right away, and forklifts in as little as 30 minutes after the completion of repairs.
For cold storage and food handling facilities, certain products can be used at temperatures down to -50 degrees Celsius for freezer use
The products have excellent abrasion, impact and chemical resistance
Damaged floor joints can be repaired and flexible joints added
Excellent for repairing damaged concrete around floor drains
Repairs are carried out with very low levels of dust and mess
Our repairs can be grinded for an even smoother surface
Improve Worker Productivity
Forklifts weighing close to 10,000 pounds can cause damage to concrete warehouse floors, leading to scratches, cracks, and missing chunks that can worsen over time.
Broken concrete in a warehouse can damage your forklift tires and slows down your productivity by either avoiding potholes or requiring extra cleaning.
Prompt repair is necessary to prevent the damage from getting worse and avoid replacement.
Delaying repairs could be more costly in the long run, as liquid can seep down into the aggregate and cause further damage.
Repairs are carried out with low levels of dust and mess and can be open to foot traffic right away and forklifts in as little as 30 minutes after completion.
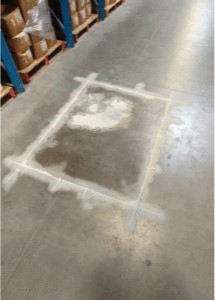
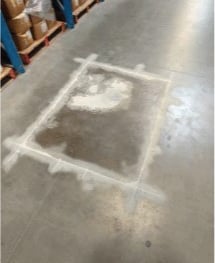
Improve Worker Floor Safety
Concrete floors that are cracked, chipped, and uneven pose a safety risk to those who are working on them, as there is a risk of tripping, sprains, and falls.
Specialized repair for warehouse/industrial floor, even at low temperatures, can be made on cracks, holes, surface wear, and trip hazards, improving safety for workers and avoiding compensation claims.
Repairing damaged floors not only protects the warehouse from further damage but also shows employees that their employer cares about their workplace, which can positively impact morale.
Hygiene - smooth surfaces allow for proper cleaning
Pitting, cracks and broken concrete accumulate contamination
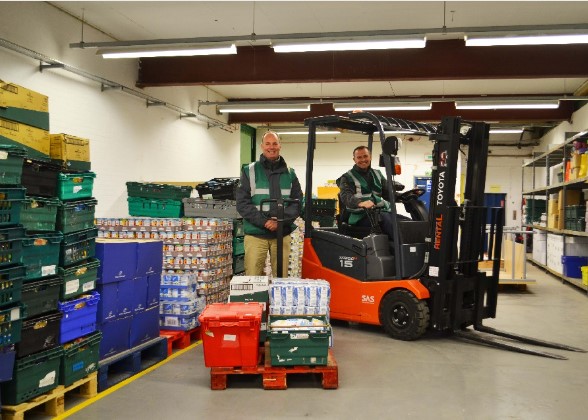
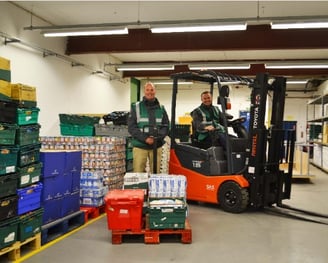
Our Process
Concrete repair process
Repair Methodology
Our highly unique and exceptional 5,800 PSI tensile strength polyurethane hybrid repair material which, coupled with my method of installation, enables a guaranteed long-term “never fail” solution.
It has an elongation 5-20% and a Shore D Hardness of greater than 80.
The polyurethane hybrid material has very quick back to service times which requires a very high skill level to install properly.
Proper installation of this 5,800 PSI tensile strength polyurethane hybrid repair material enables me to provide a guaranteed long-term “NEVER FAIL” solution for concrete problems.
I have been using this system for concrete repairs for over twelve years and have had no failures.
Four Critical Characteristics for Successful Concrete Repairs with our Proposed Repair Methodology
To see photo of the critical concrete repair process steps:
Our approach:
1) High Bond Strength: Mechanical preparation for maximized repair bonding with removal of all unsound material and rust removal and conversion when needed.
1.1 This achieves mechanical bonding by increasing the surface area and “locking in” the repair material into the concrete “landscape” or surface profile mechanically. Meanwhile, the proprietary chemistry utilized enables chemical bonding to the clean substrate. The photographs clearly show that a lot of mechanical grinding was done to remove unsound/failing concrete and to create the mechanical anchors prior to the installation of the exceptionally high strength repair material.
2) Appropriate Physical Properties: High Tensile Strength Materials with Appropriate Bonding Profiles.
2.1 Tensile Strength is required in repair areas to resist movement of the “Z-axis” (transverse or lateral) forces which create lateral stress between the repair materials and the concrete.
2.2 100% Reactive Material is required to minimize microchannels, caused by materials with water and/or solvent flashing off, that then allow surface water and moisture into the repair.
3) Reduce and Manage Hydrostatic Pressure: Strong Hydrophobic Properties (which is high water repellency).
3.1 Hydrostatic (which is water) pressure is caused by moisture coming out of and moving within hydrophilic (which is water absorbing) concrete creating pressure to lift off coatings and repairs.
3.2 Hydrostatic Pressure needs to be eliminated during and after the repair to enable long term performance.
4) Proper Substrate Preparation: Long-Term Repairs need not only clean and stable substrates but also a good substrate profile for structural mechanical anchoring.
4.1 Substrates must be clean and stable, for the repair compounds to optimize mechanical adhesion and bonding by thoroughly wetting out the substrate that possesses an appropriate “anchor” profile.
4.2 Substrate or “Anchor Profile” is the “roughness” (expressed in mils) of the concrete to be repaired; and resists the “tear off” forces generated by mechanical stresses exerted parallel and tangentially to and upon the interfacial surfaces of the concrete and the repair material(s)
4.3 Structural Anchoring must be done to ensure that the repair material to be applied in a concrete joint, crack and/or spall will have maximized longevity of the repair, employ structural anchoring which works similar to an “Anchor Profile” described above.

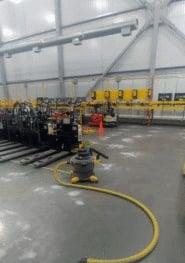
Material
Beton911 Proprietary Reactive Polyurea Repair material cures in 15 minutes and possesses 5,800 PSI (pounds per square inch) tensile strength.
Forklifts can drive over the repair after 30 minutes.
Proprietary products have no shrinkage, can bond securely to damp surfaces, cure quickly, and are resistant to moisture and corrosion.
Features:
Repairs have excellent abrasion, impact, and chemical resistance.
Proprietary two-part reactive polyurea repair and coating has no solvents, no VOC’s Polyurea is flexible and will not crack or fail in any way.
Benefits:
Cures quickly, grindable within 15 minutes after repair
No-maintenance lifecycle eliminates future repairs
Eliminates and prevents slowdowns in day-to-day operations caused by damaged concrete floors
It also has a non-slip surface
Our floor repair products are rapid curing, allowing you to reopen repaired areas after 30 minutes.
Smooth floors can reduce equipment breakdown maintenance and repair costs, as well as help with worker safety, food safety audits or certification requirements.
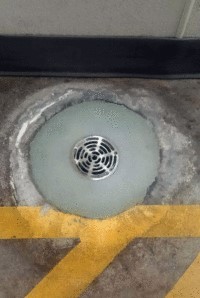
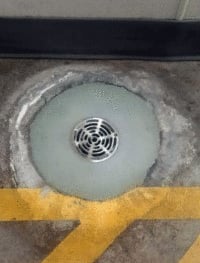
Concrete Sealing
Contaminated surfaces must be cleaned prior to the application of sealer to allow deep penetration - we have the skills and cleaning products for - greases, blood, animal by-products and wax.
Would also like to present you with my deep penetrating concrete sealer/waterproofer which penetrates up to 700 mils (0.7 inches) into the concrete making it waterproof as it obtains a chemical bond to the concrete, in addition to imparting stain and chemical resistance.
When used as a concrete repair transition material by and between old and new concrete, this system will provide a chemical bond of the new concrete to the old concrete and thus, prevent the concrete and repair from spalling. It reacts chemically with the moisture in the concrete and reacts to the concrete, producing an impermeable, polymeric composite rendering the concrete to be totally hydrophobic and not allowing any water to absorb.

